Successfully negotiating claims since 1867
Oil Recycling Facility Suffers Devastating Fire on Christmas Day
Brocklesby Limited are a leading food waste recycling company whose expertise lies in recycling edible oils and food fats for a diverse range of end user industry sectors including biofuels and energy generation. They work closely with major UK retailers and food manufacturers throughout the UK and Ireland to provide a bespoke waste management and recycling service producing in excess of 1,200 tonnes each week
When the owner and Managing Director of the long-established family business received a telephone call at home shortly after Christmas Day dinner in 2019, the news that there was a major fire developing at their extensive ten-acre site in North Cave, Yorkshire was not the type of festive cheer he was expecting to hear.
A major blaze had broken out in the tank farm oil silo storage area with hundreds of tonnes
of recycled blended oils alight resulting in significant damage to the facility. The fire
was spreading fiercely to other adjacent buildings and production areas whilst over
50 firefighters battled to save the rest of the site which converts edible oils and fats into biofuel and renewable energy products.
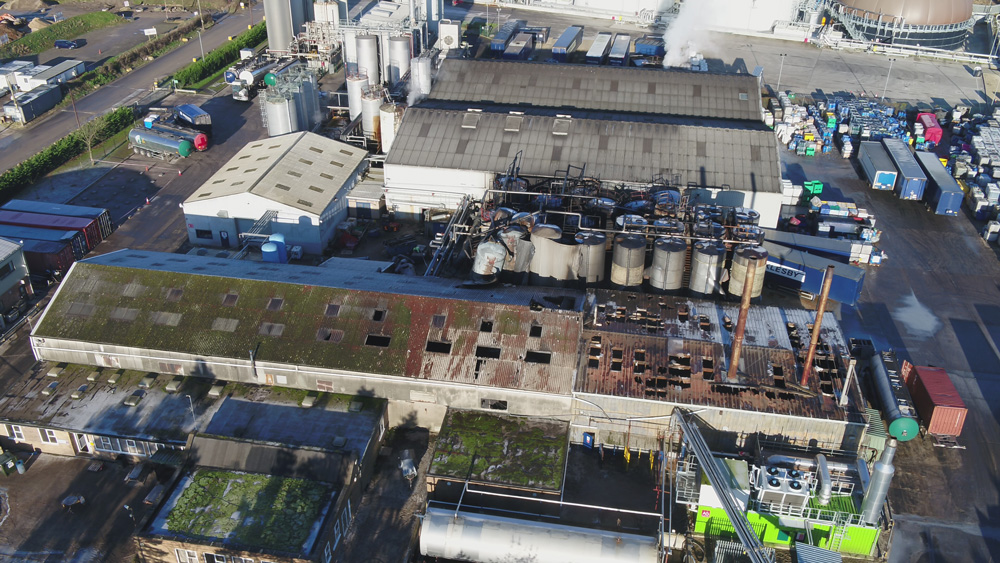
All the waste by-products brought into the business are recycled creating feedstocks for biofuel, renewable energy and green electricity from unwanted used cooking oil and fatty food waste. The facility also incorporates an anaerobic digestion plant, which has the capability to convert over 70,000 tonnes of food waste each year into renewable energy, enough to power over 11,000 homes whilst also providing enough heat energy to run
the factory.
As a result of the fire, all 27 storage vessels in the tank farm area had been destroyed as well as significant heat & thermal damage to the surrounding bunded area and concrete slab foundations. In addition, there was extensive damage to the adjacent engineering block, boiler house, processing factory and welfare/canteen buildings.
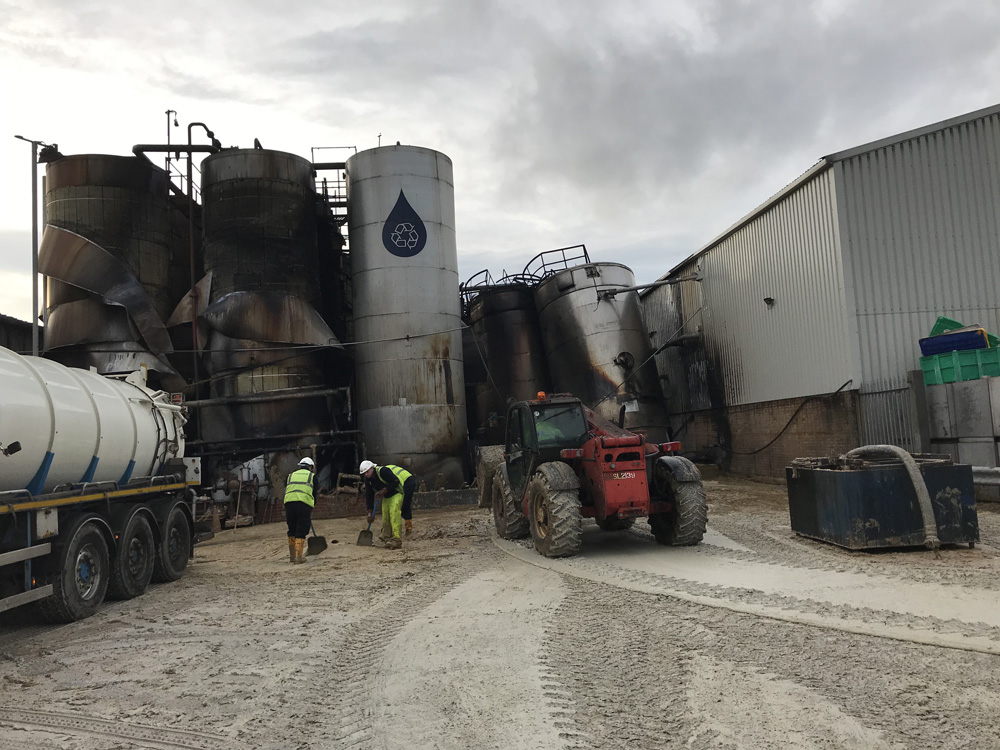
Thankfully, with it being the festive shutdown period, there was no-one harmed or injured on site at the time the fire broke out and the prompt action by the brigade meant the hazardous situation was brought under control safely over a 24-hour operation ensuring there was no immediate risk to the public or environment at the isolated site.
The ensuing damage was a devastating blow and setback to the thriving green energy business but from day one, Managing Director, Rob Brocklesby, and his team only had one thought in their minds which was to recover and rebuild the existing site and to come out of the situation stronger and make sure the business continued to expand in line with its growth plans.
The immediate priority was to preserve the jobs and livelihoods of the 75+ strong workforce at that time and a series of planning meetings and action groups were set up to commence the recovery plans whilst maintaining the “business as usual” approach to remain operational throughout the period across the remaining undamaged parts of the production facility.
A massive clean-up and debris removal operation commenced to remove the hundreds of tonnes of congealed oils, fire residues & large volumes of extinguishment water which had deluged the site, including pumping out interceptor tanks, roads, drains and gullies. However, thankfully the prompt action and assistance from local specialist restoration contractors over the coming week’s helped to prevent further contamination ensuring the environmental impact was expertly mitigated.
In terms of the resulting Insurance claim and Business Continuity/Disaster Recovery support, the Thompson & Bryan team were quickly engaged to represent the policyholder’s interests providing them with the services of their own specialist loss adjusters. The multi-disciplined team worked in close collaboration with the client’s management and the brokers, Towergate, every step of the way to ensure the business interests were protected at all times whilst enabling the client to focus on resurrecting their business, rather than having to prepare detailed claim documentation themselves.
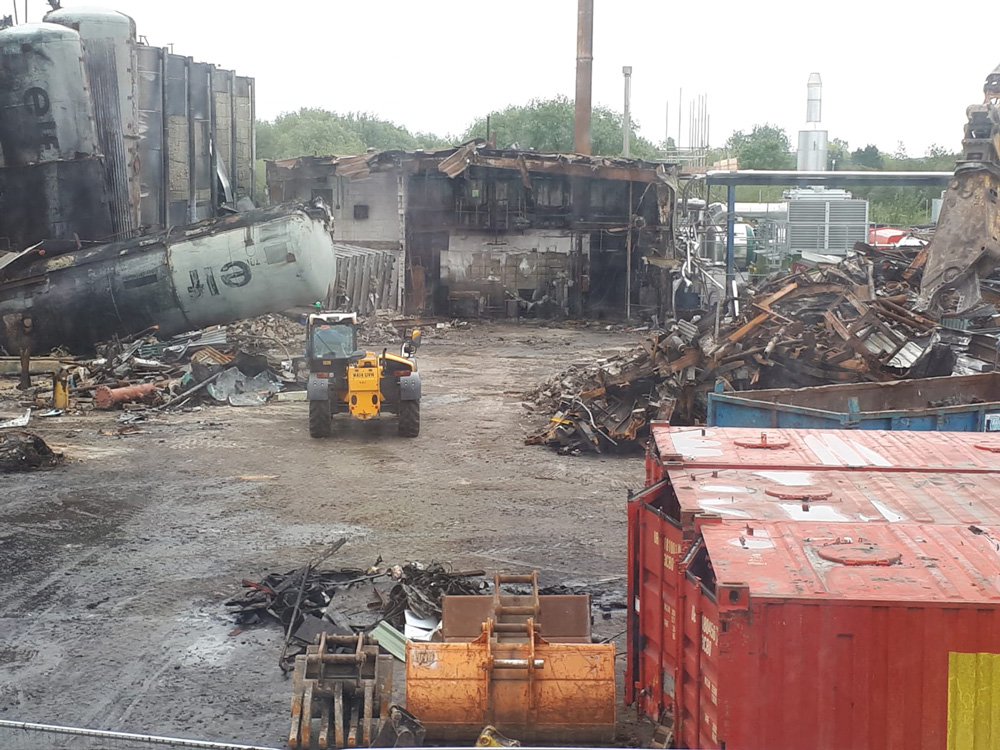
Extensive forensic scientist and loss adjuster investigations were undertaken during the immediate aftermath of the fire with close co-operation and management of the process by our team of experienced professional advisors to make sure that an acceptance of liability and engagement of the policy was fast-tracked. This gave the business the necessary backing and financial support it needed to survive with interim claim submissions and payments on account secured at the earliest possible stage.
On the Business Interruption side, the significant forward order contracts with major customers were prioritised wherever possible to safeguard the bulk of the annual turnover with the use of ‘increased cost of working’ mitigation measures such as off-site bulk tank storage, hired in temporary boilers and overtime working/additional shifts to ensure the continued operation of the site.
At the same time, the incoming logistics and supply of used cooking oils, other fats, and waste food products ready for onwards processing had to be maintained to meet ongoing commitments and protect the long-term supply chain. Without the tank farm area, a variety of temporary measures were put in place including the use of additional IBC’s, Dolav’s and other containers together with some carefully managed off-site processing using outside sub-contractors.
The financial aspects of the loss were handled by our forensic accounting team and involved in depth statistical analysis with a multi-faceted approach to present the claim in the most beneficial way.
The knock-on effects of the fire and working inefficiencies created by the need for temporary site reconfiguration and other
mitigation measures meant that the business became impacted in several different areas. Accordingly, the Business Interruption claim involved many complex calculations across a variety of departments and processes to analyse the effects on the working Gross Margin, as well as the standard turnover, sales losses, gross profit, and increased costs of working.
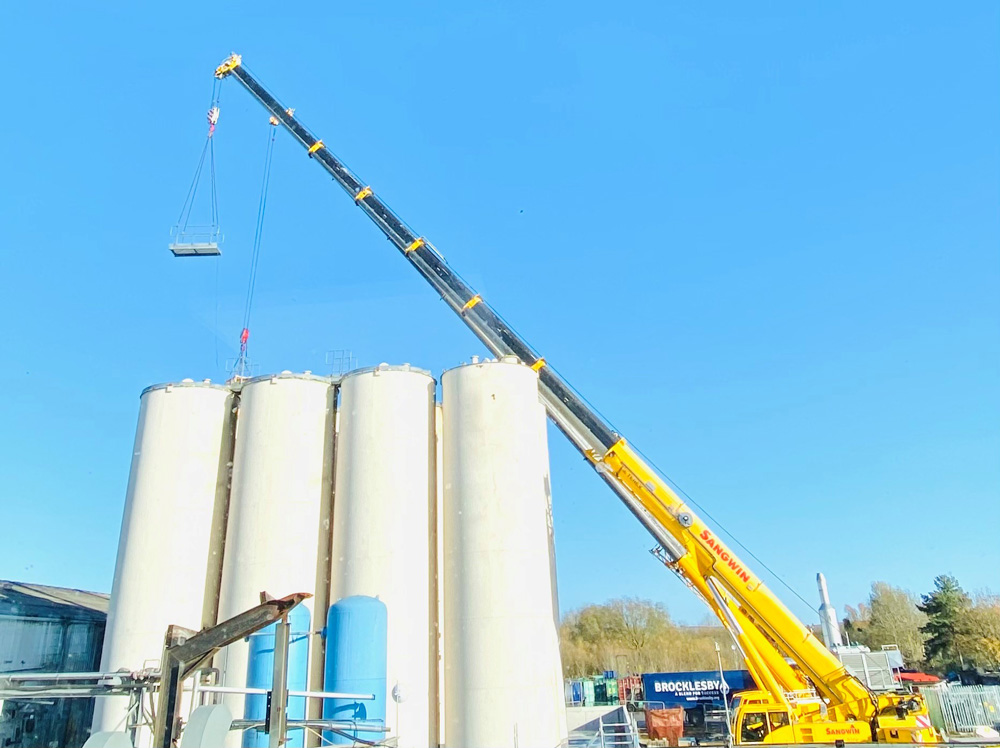
This encompassed many thousands of hours of experts’ time with trends and sales forecasting, yield projections, management account profit & loss analysis, business modelling and costs and expenditure analyses.
On the flip side insurers engaged the services of their own accountants to challenge and adjust the financial claims put forward so this became a crucial area of the overall negotiation. Ultimately, over 50% of the total claim settlement was dependent upon this element of the claim alone so this played a huge part in the added-value service we were able to provide.
In addition, all the other aspects of the claim were co-ordinated concurrently to collate and quantify the material damage losses across Buildings, Machinery & Plant, Computers and Stock with regular progress meetings and interim payment requests put forward and negotiated in a timely manner by our surveying and assessment team to allow the onward momentum of the recovery and reinstatement project.
When a major & complex claim occurs of this nature, it is imperative to have a robust risk-management led bespoke suite of policy covers arranged by an experienced and hands-on broker partner. This creates the basis of the contract in force which ultimately determines the parameters under which the claim can be settled, so must be carefully planned, and implemented to produce the optimal policy programme with sufficient levels of cover, sums insured, and limits of indemnity all arranged with suitable and financially stable insurer markets.
Although the incumbent brokers had only recently commenced their work with the client just prior to the last renewal, the comprehensive Insurance programme already put in place by Towergate was able to be utilised throughout the claim management process to optimise the outcome of the claim.
Furthermore, as with any major loss scenario, there are always certain aspects open to interpretation, however through experience and many years of technical knowledge and expertise the Thompson & Bryan loss adjusting team were able to ensure agreement under all aspects of the claim on the best possible terms for their client.
Over a period of twelve months, extensive and detailed work on policy interpretation, financial analysis, negotiation, and co-ordination with other professionals involved on the project to optimise the amount of the insured recovery under the terms of the policy resulted in a successful final claim settlement in excess of £6M with the balancing payments paid out by insurers during the early part of 2021.
Client Testimonial
“We appointed Thompson and Bryan (UK) Ltd to act for us during a significant fire claim. During the challenging time for the business Thompson and Bryan offered significant support and guidance and were an invaluable partner in the process.”
“The outstanding attention to detail and level of understanding of our business the team showed must be applauded.”
“If you need a committed and professional company, I would highly recommend them.”
Neil Taylor, Managing Director
Brocklesby Limited
Despite the numerous challenges Brocklesby faced due to the fire and the global Covid-19 pandemic to contend with at the same time, the business continues to grow and expand its position within the sector as one of the UK’s leading waste oil recycling companies.
Manoeuvring quickly to manage both crises, they were able to continue to operate and support customers, many of which were large food manufacturers critical to pandemic efforts, while simultaneously initiating the rebuild and expansion of the North Cave site following the fire.
As part of the site rebuild programme aided by the Insurance reinstatement funds and claim settlement achieved, continued capital investment has enabled a move even further towards environmentally conscious working practices with the installation of a new mains gas pipeline to produce cleaner steam driven production lines rather than burning oil. The business has installed the most energy efficient boilers with steam recovery in the form of economisers and Reverse Osmosis to reduce the amount of wasted energy making the site greener and more energy efficient than ever before. The Directors also took the opportunity to upgrade the rest of the site including a new larger tank farm, a state-of-the-art control room, new weighbridges, goods in/out docking and operations facilities to help drive through operational efficiency improvements with the site refurbishment finalised in early 2022.
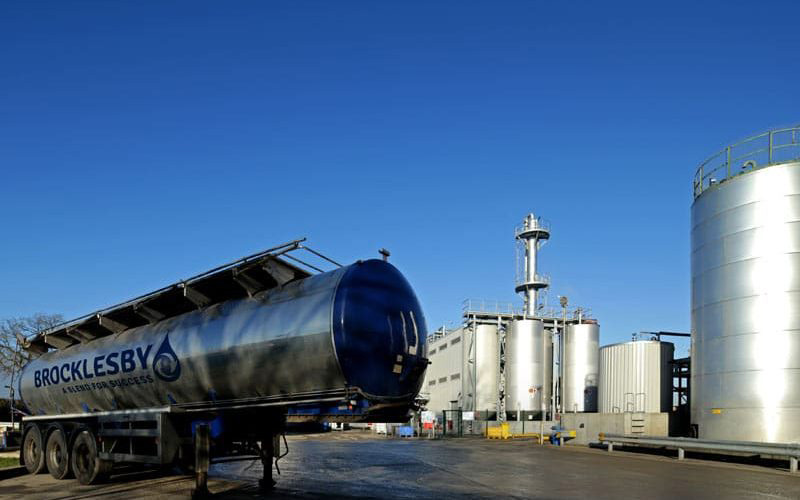
The company’s commitment to cutting carbon emissions and improving the environment was recognised by Investors in the Environment’s Green Award, the highest achievable level, and the Hull Daily Mail 2019 Business Awards, where it was awarded the Green Award in addition to being nominated as finalists again in consecutive years.
During Q1 2022, Energy company St1 Nordic Oy acquired 100% of Brocklesby Ltd and the business with a strong 35-year history behind them now employs over 80 staff turning over more than £63M per annum and is continuing to grow its reputation and reach as a truly market leading recycling and sustainable energy provider.
We are proud to be associated with such an established and progressive business who have shown incredible levels of resilience with strong leadership and a highly collaborative team to enable us to play our part in this success story.